Self Cleaning Screen Meshes
The anti-clogging screen surfaces are composed of wavy wires arranged side by side. With this wire sequence, square apertures are formed. The wavy wires are interconnected at certain intervals with an extremely abrasion-resistant and flexible polyurethane.
Specifications of Anti-Clogging Screens
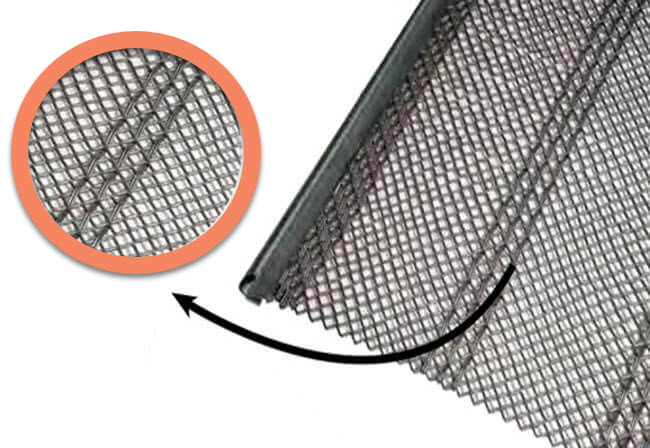
The distances of these transverse connections are variable and can be produced according to need.
The non-clogging sieves for working screening machines vibrate in themselves as well as machine vibrations thanks to their flexible wires. In this way, sticking and clogging of the apertures of the sieve is prevented to a great extent.
The square sieve maintains its shape and offers a very clean screening and classification efficiency.
Polyurethane screens make a difference with longer life, more open screening area, less adhesion in the transverse connection parts, and additional cross-member protectors.
Anti-clogging screen wires are recommended to be used when there are screening problems with square mesh screens. Anti-clogging screens are made of round wire. The round wire model has the feature of preventing blockages and adhesions, especially with its own internal vibration.
TYPES OF ANTI-CLOGGING SCREENS:
Diagonal H(Harp)-Type Anti-Clogging Screen
H-Type Poly Ripple Wire Mesh Screens are made from high carbon or stainless steel molded in place with high wear-resistant, flexible polyurethane. This long slot configuration spaces provide a greater open area that could maximize material through-put in screening. The rugged polyurethane profiles anchor the wires securely in place, allowing the H-Type Poly Ripple Wire Mesh Screens to withstand a larger feed material and loads than other straight weft screens.
P(Piano)-Type Anti Clogging Flex Screen
In this type of sieve, long gaps were obtained by using only completely straight wires. Since the wires of this sieve are not twisted, it can be made by choosing from a wide variety of materials.
T(Triangle)-Type Anti-Clogging Screen
This screen consist of alternately arranged straight and crimped wires, which crimped horizontally to the screen level as well. By adding straight wires, triangular screen openings are created. The screen wires are also fixed at definite spacings by cross-bindings made of high wear-resistant, flexible polyurethane. The straight and horizontally crimped wires provide a flat surface for reduced friction and extended wear life. The straight wires make the screen stronger to take heavier loads. During the screening process, the crimped and straight screen wires perform different oscillations. This ensures a screening operation largely free of blinding, especially with moist or sticky materials. The polyurethane cross-bindings ensure a longer service life, a larger open screening area, a reduced amount of adhesion of the material to the narrow cross-bindings, and additional protection of the support.
W(Wave)-Type Anti-Clogging Screen
The W-type delivers maximum throughput and is ideal for the removal of fines, which produces a cleaner retained product. Overall blinding is significantly reduced when screening wet adhesive materials. The W-type can also be used to produce high volume dry products in certain applications. Not to be used when it is important to retain chips, silvers, and elongated materials.
For extremely sticky applications in which D-type will not achieve a sufficient cleaning effect, a wave design can improve the situation. W-type offers maximum cleaning action and is capable of handling more moisture than D-type and T-type.
• High open area
• Exceptional cleaning ability
• Suited for applications with a high percentage of near-size material which is prone to pegging or blinding
• Used for declogging very sticky materials with no flacky products
• Removes fines, produces a cleaner retained product and reduces blinding of wet and sticky materials
W(Wave)-Type Double Wire Anti-Clogging Screen
This type of sieves, which are in the same shape as the diagonal type sieve, are formed by laying an extra row of wires in addition to the normal arrangement to gain strength in heavier conditions.
MATERIAL OF ANTI-CLOGGING SCREENS:
High carbon steel wire
Chrome nickel (AISI 304-310-316)
Use temperature Max 80 ° C
Abrasion Resistant Polyurethane.
Advantages of Anti-clogging Screens
-
By removing standard screen mesh lock-up points, anti-clogging screen mesh is thinner, by this means it has better screening capability and abrasion-resistant because the friction level is minimal.
-
30% more capacity than woven wire
-
Polyurethane bands over the screening surface area exposed to maximum friction. But these polyurethane bands have an almost unlimited life.
-
These vulcanized polyurethane bands constitute one unit with the warp yarns, thanks to this the friction between fine particles and screens is prevented. And this prolongs screen mesh’s life.
-
This type of screen meshes prevents clogging of thin, moisture, or clayish materials.
-
Decreases or almost prevents clogging of the screen meshes by overlapping of the materials.
-
It increases the productivity of small scale vibrating screens.
-
It allows the screening of corrosive thin materials and ensures wearing resistance.
-
To ensure functionality and long life, polyurethane bands must come down on the vertical and horizontal carriers.
-
Anti-clogging screen meshes must be tensioned.
-
High performance and excellent self-cleaning, longer wear-life
-
This design also ensures decreasing in the tension of wires, thanks to this the screen becomes more flexible and the quality of vibratiıng increases.
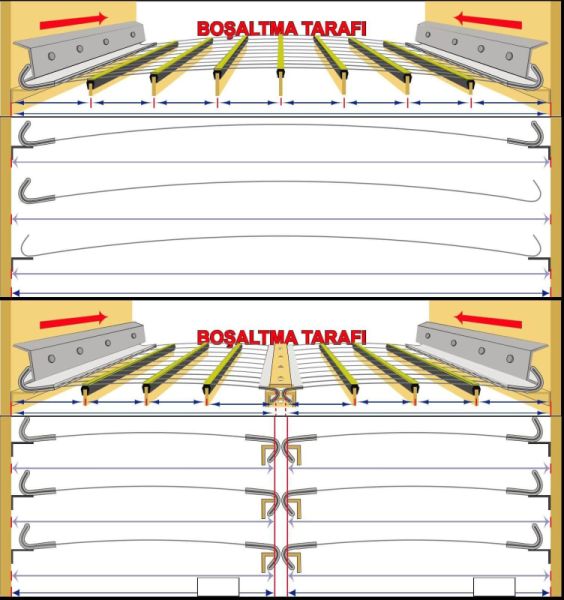
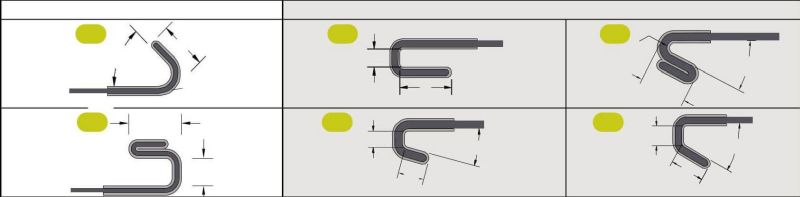
How Anti-Clogging Screens Create a Composite Structure?
- Wires are used as high strength spring steel (DIN 17223). Wires are the structure that forms the sieving surface.
- Abrasion-resistant polyurethane is the material used to bind wires.
As an example, you can examine the Aperture - Wire Diameter - Open Screen Area Table.
Aperture [mm]
|
Wire Diameter [mm]
|
Screen Opening [%]
|
3 mm
|
1,8 mm
|
50%
|
4 mm
|
2 mm
|
47%
|
4,5 mm
|
2 mm
|
50%
|
5 mm
|
2 mm
|
52%
|
5,5 mm
|
2 mm
|
54%
|
7 mm
|
2,2 mm
|
60%
|
10 mm
|
3 mm
|
48%
|
SETAŞ GROUP
Self Cleaning Screen Meshes
SETAŞ GROUP is a company that has proven its experience and success in the sector with the concepts of "quality, service and sustainability" with its flawless service approach since its establishment with the brand KESTAŞMAK. We will also offer you suitable solutions for your product requests.
As KESTAŞMAK, our goals are; to be a dynamic solution partner that develops innovative products and services, adding value to the industry and its stakeholders with the understanding of "ensuring the continuity of quality" and "keeping our customers at the center of all our processes, meeting their demands on time and with high quality".
SETAŞ GROUP, which always aims at customer satisfaction. You can reach us by calling our call center at
+90 (535) 047 1230
and get detailed information and offers.